top of page



Search


The Smart solution to stop lubrication related bearing failures
If you ever had a lubrication related bearing failure you need to have a look at the UE Systems OnTrak SmartLube System. The OnTrak...
Admin
Jan 17, 20211 min read
Â
Â
Â


Another example where Ultrasound adds value
One of the more interesting cases I worked on was when I took ultrasound readings on the bearings of a slow moving (about 9 RPM), large...
Admin
Oct 29, 20192 min read
Â
Â
Â


First production modules of Ultra-Tek GSM4G now available
Ultra-Tek are excited to announce the arrival of the first production models of the GSM4G unit. This mobile phone linked Ultrasound...
Admin
Oct 21, 20191 min read
Â
Â
Â
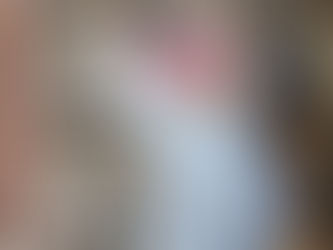

What's all the noise about Ultrasound
Airborne & Structure Borne ultrasound have been gaining tremendous popularity over recent decades and is no longer a technology only...
Admin
Oct 4, 20191 min read
Â
Â
Â
bottom of page